RFID Solutions for Manufacturing Operations
RFID in Manufacturing Operations - Production Process & Inventory Control
RFID in Manufacturing
“Measurement is the first step that leads to control and eventually to improvement. If you can't measure something, you can't understand it. If you can't understand it, you can't control it. If you can't control it, you can't improve it.” H. James Harrington
This is the underlying principle behind the vision of Digital Transformation. AssetPulse's RFID for manufacturing solutions enable organizations to achieve this vision.
IoT including RFID and BLE sensors, coupled with the AssetGather platform can aid in optimizing manufacturing processes to reduce time and cost, while improving decision making and increasing efficiency.
The manufacturing industry has succeeded in applying a dizzying array of technologies to gain improvement in throughput and operational efficiencies. As the industry tries to maximize its margins, it has to address the still-significant gaps in supply chain and operational visibility along with sobering inaccuracies that still plague the production lines. These gaps and inaccuracies have varying impact, depending on the vertical. E.g. Lack of traceability in the Biomedical Device industry can have debilitating consequences as opposed to in a plastic molding line, which can handle relatively higher tolerances. RFID can bridge the gap between manufacturing execution systems (MES), enterprise resource planning (ERP) systems and the floor. AssetPulse RFID solutions have the ability to provide data at a much greater level of accuracy, timeliness and detail.
RFID in Material Inventory Management and WIP Tracking
Leveraging RFID in supply chain is well understood. From the processing of the ASN, Receiving, Inspection, Put-away and Raw Material Fulfillment/Replenishment, AssetPulse RFID solutions can be used to increase automation and eliminate manual errors.
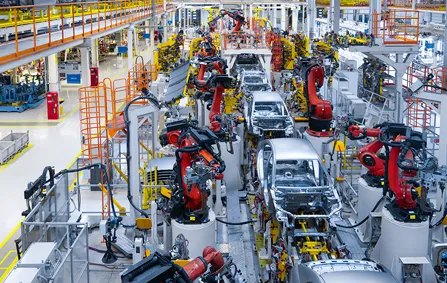
A bigger bang for the buck can be realized by applying RFID in manufacturing processes other than Material Handling. Today, there is limited visibility into most operations. There are several areas where AssetPulse can help organizations become a more data-driven enterprise, thereby increasing operational efficiencies, optimizing floor schedules, improving production planning and preventing errors:
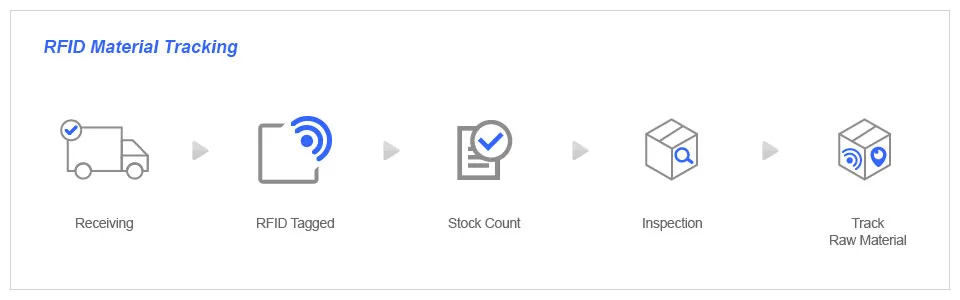
-
Traceability of raw material and components - from warehouse to production line, facilitating optimized JIT inventory management, helps in monitoring wastage and shrinkage
-
Efficient Empty-bin Replenishment Management
-
Tying the Lot# and Batch# data of raw material to the product itself, for increased traceability
-
Work Order Tracking
-
Tracking technician time at each work cell - know who worked on what and for how long
-
Tracking WIP product along with associated travelers
-
Tracking Finished Goods - in the Distribution Center
-
Finished Goods on Consignment at the Customer Site
RFID in Production Equipment and Tool Tracking
Other essential processes that are tightly coupled with the manufacturing line include management of tools and equipment. With more of the focus on the product itself, visibility of the tools and equipment on the line is very limited. AssetPulse solutions can be used to track:
-
Actual tool and equipment inventory on the line - what is used, where and on what product
-
Management of calibration, PM, repairs and safety inspections
-
Identify unutilized tools and equipment, thereby helping in optimal asset utilization
-
Movement of tools and equipment within the line, when tool used in the wrong location can lead to high impact quality errors
-
Tracking onboarding of new equipment and disposal of obsolete equipment
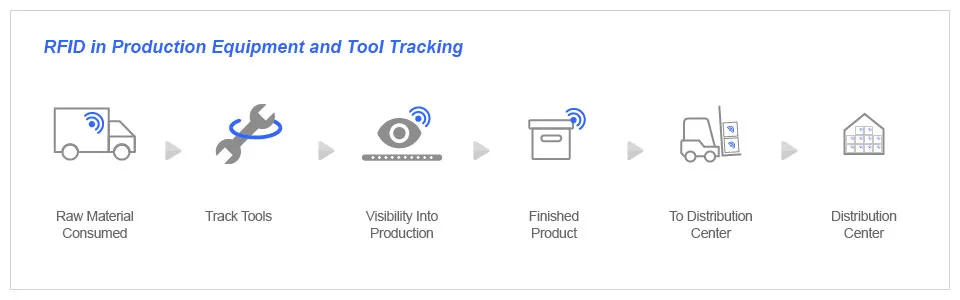
Finished Goods
AssetPulse's RFID tracking system for manufacturing can be used to track Finished Goods, from the end of the production line, to Inspection, Quality and finally shipping out to the Warehouse or Distribution Centers. Several compliance and traceability driven processes like creating Device History Records for Biomedical devices, can be efficiently executed with AssetPulse solutions. Monitoring the beginning and/or end of each of these phases, can provide insight into operational bottlenecks, roadblocks and other inefficiencies that have hitherto lay hidden.
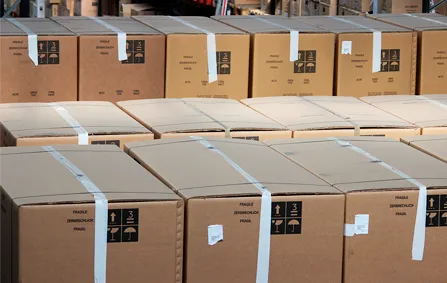
Post production, Finished Goods can continue to be tracked to and at the Distribution Centers and Warehouses. Further, they can continue to be tracked at the Distributors and Customer Sites, especially when they are shipped on Consignment to these locations.
Quality Control
Every industry tries to maximize quality metrics using processes that increase automation and accuracy. Quality processes permeate every phase of manufacturing. E.g. AssetPulse's RFID solutions can be used to ensure correct and timely use of raw materials on the manufacturing line, they can help ensure a FIFO process for raw materials that have a limited shelf life. Quality metrics can be collected all through the process with AssetPulse’s RFID for manufacturing solutions that provides data for statistical and root cause analysis. All paper-based processes can be aided by RFID tagging the documents to enable automated and reliable traceability and tracking of these important documents.
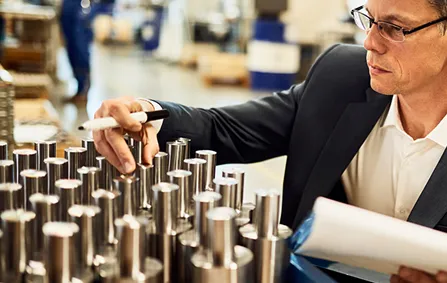
Integration with MES and ERP systems
Most enterprise manufacturing facilities are instrumented with Enterprise systems to aid in manufacturing. AssetPulse's RFID solutions have several integration touch points to facilitate bi-directional flow of data to and from such systems. Given that AssetPulse's RFID tracking system for manufacturing provides a real-time view of the physical location of the assets being tracked, exception events can also be communicated to the Enterprise applications.
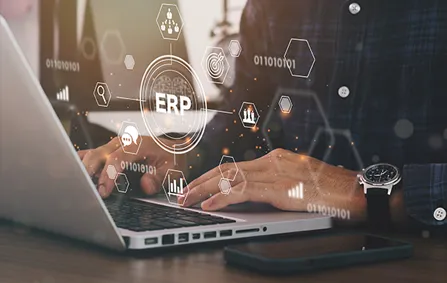
AssetPulse RFID in Manufacturing Operations
The solutions comprise of the following:
-
AssetGather Server software to visualize, report and alert on all aspects of manufacturing operations
-
AssetGather Mobile software on the handheld RFID Reader
-
AssetGather Adapter software managing the fixed RFID readers
-
RFID tags rugged enough to withstand the challenging manufacturing environments

RFID Tags for Manufacturing Sector
WIP product, tools and manufacturing equipment are all items that can be tagged with RFID inventory tags. However, one unique requirement of these tags is that they need to withstand extremes in temperature, pressure, moisture and chemical exposure, in addition to shock, vibration and mechanical impact. AssetPulse has a wide variety of tried and tested RFID tags to address such challenges.
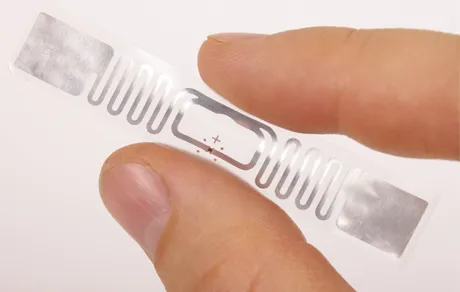
RFID Readers
Manufacturing environments can also require ruggedized RFID hardware - both handheld and fixed readers and antenna. Handheld readers have to withstand being dropped on concrete floors or being exposed to moisture, among other challenges. Fixed readers and antenna need to not only tolerate wide temperature ranges, but also withstand dust or moisture exposure or outdoor conditions. AssetPulse offers a wide selection of readers, antenna, cables etc. suitable for manufacturing environments ranging from sterile clean rooms to heavy engineering factories.
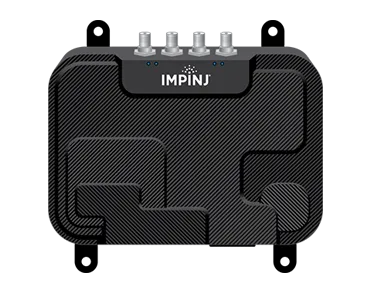
Benefits of using RFID in Manufacturing
- Gain visibility of your WIP manufacturing floor to eliminate inefficiencies and quality issues
- Receive exception alerts when errors and suboptimal events occur
- Maximize throughput
- Maximize efficiency of manufacturing labor
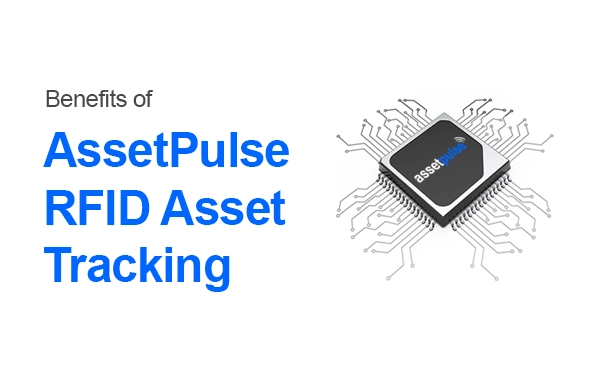
Case Study
An aerospace manufacturer has successfully implemented the AssetPulse RFID solution to track over 10,000 tools that are used throughout their factory floor and in their warehouse. One of the many benefits realized by the customer is vast improvement in efficiency. Earlier it would take anywhere between 15 minutes to 2 days to locate tools. Now, it takes less than 2 minutes!
Frequently Asked Questions
By leveraging RFID technology, manufacturers can gain improved visibility across the entire production process. It allows for tighter control of materials and finished goods, while enhanced work-in-progress (WIP) tracking helps optimize production flow. Additionally, RFID streamlines asset tracking of tools and equipment, minimizing loss and downtime. This overall improvement in efficiency and reduction in errors leads to better quality control and compliance with industry regulations.
- Know exactly where all your WIP is, at all times?
- When it entered a department/workstation/area and when it was moved from there? Know how long it stayed.
RFID brings real-time inventory transparency to the manufacturing floor. By constantly monitoring stock levels, manufacturers can identify and address shrinkage issues, eliminate errors from manual inventory, and leverage accurate data for improved forecasting and production planning. This translates to a more efficient and streamlined operation.
RFID automates asset tracking in manufacturing, facilitates automation, thereby eliminating the need for manual processes. This real-time visibility into the location and status of WIP, tools and equipment, empowers faster decision-making and increased agility to adapt to production changes. Consequently, labor costs associated with manual tracking are reduced, while manufacturing processes, asset utilization and equipment usage are optimized. The result is a more streamlined and responsive manufacturing environment.
Embedded RFID tags automatically identify materials WIP and assets, capturing real-time data that seamlessly integrates with manufacturing execution systems (MES) and ERP systems to automate workflows. This enhanced data accuracy fuels more efficient automated processes, ultimately minimizing downtime and maximizing throughput.
RFID goes beyond mere inventory control; it becomes the eyes within your production process. Attaching tags to work-in-progress (WIP) items unlocks real-time visibility of their movement throughout each stage. This valuable data empowers manufacturers to identify bottlenecks that act as roadblocks to production. They can use this information to fix any slowdowns in production. This helps them make a better schedule and get finished products to customers on time.