RFID Work Order Tracking System to Streamline & Optimize your Manufacturing Process
RFID Work Order Tracking Software for Real-time Visibility, Accurate Data, and Improved Efficiency
RFID Work Order Tracking System for Streamlined Production Process
A work order in manufacturing is a document that contains the instructions, materials, and resources required to complete a specific production job or task. It typically includes details such as the job description, quantity of the product, raw materials or parts required, the labor required, deadlines, and any other relevant information.
Work orders are typically created at the start of a job and closed when the job is completed. Work order tracking is essential to track the progress of a job and ensure that it is completed on time and to the required specifications, thereby meeting certain quality standards. Work orders are created from various sources such as customer orders, internal requests, and production plans, and they may be used by various manufacturing functions such as production planning, production control, quality control, and accounting.
Work orders are used in a variety of manufacturing settings, including machine shops, assembly lines, and other industrial environments.
Challenges in Work Order Tracking
There can be several challenges when it comes to tracking work orders in the manufacturing industry, including:
- Accuracy and Integrity of Data: Data collection is usually done manually, requiring the technician at each station to scan or enter something on a paper form or electronically. Therefore, many questions arise - Did all the data get collected? Is it accurate? Any errors or omissions would affect production and scheduling, as well as result in potential quality control issues. This process is of course, subject to human error, which can result in glaring inaccuracies.
- Manufacturing Process Complexity: Manufacturing processes can be complex - including many interwoven tasks and operations. Keeping track of work orders can be very challenging. This is especially the case, when there are multiple parts to the work order and each part's status has to be captured in the work order. In this context, the work order status could be incomplete, because it is missing the status for a subset of parts.
- Real-time Status of the Work Order: Often, during the manufacturing process, there is a need to determine the status of the work order - what has been completed, where are all the components of the work order and how much is left for completion. That level of granularity is difficult to provide with any degree of accuracy, when manually tracked, especially when dealing with a high volume of work orders.
- Physical Work Order being Misplaced: Many manufacturing processes are still being run with physical paper-based work orders. These could be sheets of paper stapled together or sheets of paper in some form of envelope. These Travelers sometimes tend to get misplaced. A lot of hours are spent looking for the work order. Not only is this a waste of resources, but more importantly, it can stop production and delay delivery dates.
RFID Work Order Tracking System for Manufacturing
Having worked with several manufacturing customers across various industries, including industrial manufacturing, medical devices, electronics, etc., AssetPulse has designed and developed an RFID Work Order Tracking System specifically to address issues related to work order tracking in manufacturing.
RFID is an optimal technology for manufacturing. Not only does it solve the tracking issues very efficiently, but also it is cost effective. Further, since RFID tags are available in various levels of ruggedness, they can be used effectively in all kinds of manufacturing. It is important to note that RFID is not only very suitable for work order tracking and Traveler tracking, but it lends itself well to solve other tracking needs including raw material tracking, tool tracking, WIP Tracking and even personnel tracking.
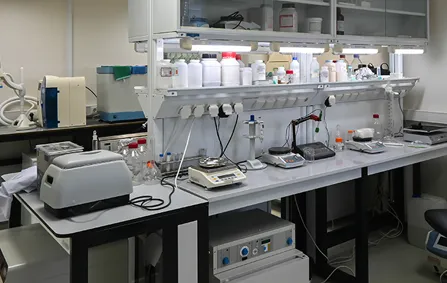
RFID Work Order Tracking Software for Real-time Visibility
RFID technology can track work orders in real-time, regardless of where the work order is, in the production process. For example, if a work order is delayed or stopped at a certain stage, the system can automatically notify the appropriate personnel, and allow for quick corrective action to be taken.
AssetPulse's RFID work order tracking software can provide significant benefits to manufacturing companies by providing real-time visibility, improving accuracy, and efficiency in the tracking and management of work orders. It can help to reduce costs, improve production planning, and ultimately increase profitability.

Work Order Tracking System - Seamlessly Integrates with Other Systems
AssetPulse's RFID Work Order Tracking System seamlessly integrates with other systems such as Enterprise Resource Planning (ERP) and Manufacturing Execution Systems (MES). This can provide further benefits such as improved inventory management, streamlined production planning, and better customer service. With the integration of RFID technology, the work order tracking software can accurately track the location and status of work orders, raw materials, tools, and even personnel in real-time. This allows for better management of resources and can help to streamline and optimize production processes, reduce costs, and increase efficiency. AssetPulse has a great deal of experience integrating with a variety of enterprise applications including SAP, Oracle, Maximo, etc.
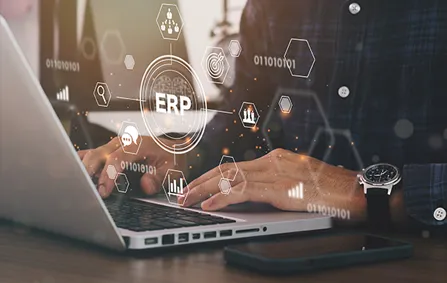
Benefits of Work Order Tracking using RFID
RFID tags are attached to work orders and as they travel through the production process, RFID readers are used to track their location and progress. An RFID reader can be placed at each step on the production floor and as the work order moves from one step to another, the location, timestamp and duration is recorded - automatically, without the need for manual intervention or data input. This helps in providing unprecedented accurate visibility into parts of manufacturing processes that were hitherto opaque. Some of the insight includes:
- Timestamp of when work order enters and exits a location on the factory floor
- Duration a work order stayed at a location
- Last known location of work order - important when it is misplaced
- Route of work order as it is moved through the locations
- Locations of parts of the work order, if it consists of multiple parts
- All the above data can be used to determine percentage completion of a work order
- Bottlenecks that impact manufacturing efficiency can be detected with the above data
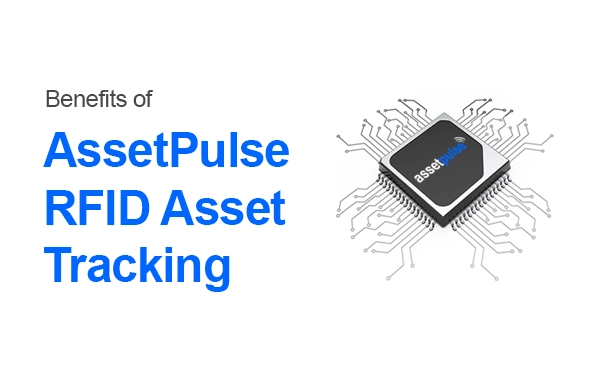
Frequently Asked Questions
Work order tracking is the systematic monitoring of jobs throughout their lifecycle, from creation to completion. It ensures each task is executed as planned, on time. It goes beyond task management, including updating status, managing inventory, invoicing, and coordinating across departments. Effective tracking ensures tasks are completed in the right order, technicians are dispatched efficiently, and no job goes unnoticed.
Tracking work orders provides a holistic view, aligning the right technician with the right job and ensuring timely parts delivery. This minimizes wasted effort and boosts customer satisfaction by enabling quick fixes and real-time updates. By optimizing resources and time management, manufacturers gain a competitive edge through operational excellence.
A work order tracking system is essential for effective inventory management. It ensures raw materials, components, and finished goods are allocated correctly based on production needs. This prevents stockouts, optimizes reorder points, and maintains accurate inventory counts, leading to smoother production and minimized waste.
Real-time tracking empowers manufacturers to provide accurate updates to customers. When clients inquire about order status, manufacturers can promptly share information on progress, estimated completion times, and any delays. This transparency builds trust and enhances overall customer satisfaction.
Real-time work order tracking empowers departments to collaborate seamlessly. Production prioritizes tasks, maintenance gets repair alerts, procurement orders precisely, and quality control monitors progress. This teamwork helps track work orders efficiently, streamlines operations and yields better results.
Modern work order tracking systems conquer complex workflows with features like multi-level work orders (breaking down big jobs) and dependency management (ensuring tasks happen in the right order). They also allow for parallel processing (doing related tasks simultaneously) and customization to fit specific manufacturing needs. This all leads to efficient execution and smoother operations.
Unlike traditional methods, AssetPulse's RFID Work Order Tracking System provides real-time visibility throughout production with material tracking via RFID tags. This accuracy leads to faster issue identification and better decisions. Additionally, RFID streamlines production by quickly locating work orders, boosting efficiency. It also integrates seamlessly with existing systems, improving inventory management, planning, and customer service. In essence, AssetPulse's RFID work order tracker system revolutionizes manufacturing with real-time data and efficiency gains.